Conductors

Besides the importance of shielding techniques, grounding configurations and insulation materials, a cable manufacturer should equally take into account a number of parameters that will help in controlling the electrical characteristics of conductors in order to achieve optimum performance in any given application.
The proper contaminants of high purity copper, silver and gold, and the efficient combination of both solid-core and multi-core wires, effectively exploit the advantages of these metals and helping our conductors to provide relatively lower resistance a given thickness.
Our hybrid conductors will help audio devices to reveal their sonic characteristics, to deliver signal without adding unwanted colorations and to stimulate the original sound of instruments with impressive accuracy.
One of the determinant parameters for the effectiveness of a cable is the electrical conductivity of signal conductors. Electrical conductivity is the ratio of the current density to the electric field strength and it measures how well a material can accommodate the movement of an electric charge. The values of electrical conductivity are measured in units of SI (Siemens per meter), but they are also reported as a percentage of IACS (International Annealed Copper Standard). The conductivity of annealed copper (annealed copper standards: density of 8.89 g/cm3, length of 1 meter, weight of 1 gram and resistance of 0.15328 ohms) is the benchmark and it is defined as 100% IACS at the temperature of 20°C. The conductivity values of all other materials are measured as a percentage of IACS compared to the value of annealed copper. The below table presents a classification of metals according to their conductivity values as a percentage of IACS:
CONDUCTIVITY (as % of IACS at 20oC)
METAL
Silver 105%
Copper 100%
Gold 72%
Aluminium 61%
Magnesium 39%
Zinc 28%
Nickel 25%
Cadmium 23%
Cobalt 18%
Iron 17%
Platinum 16%
Tin & Ph. Bronze 15%
Lead 8%
Ni Al. Bronze 7%
Steel 3 to 15%
By reading the data of the table, we can assume that copper, silver and gold are excellent conductors of both electricity and heat and the best way to increase their electrical and thermal conductivity is to decrease their impurity levels. Nowadays, the cable industry has amazingly improved the processing techniques of these metals, offering purity levels that exceed standard values reported on the list of IACS. A good example of that could be a copper conductor of 99.99997% (6N) purity that is able to provide a greater conductivity levels than the benchmark value of the annealed copper, approaching even the IACS value of silver.
Electrical resistivity is the reciprocal of conductivity and it measures the opposition of a material to the flow of an electrical current that passes through it, resulting in change of electrical energy into heat, light, or other forms of energy. The electrical resistivity is measured in ohms per meter (Ω/m) and the resistance values of a conductor depend upon four main variables:
1. The first variable is the length of the conductor which will affect the total amount of resistance, where the longer the conductor is, the higher the resistance will be.
2. The second variable is the cross-sectional area of the conductor which will affect the amount of resistance, where the higher the cross-sectional area of a wire is, the less resistance to the flow of electric charge will be.
3. The third variable is related to the type of metal (or metals) that the conductor consists of. As stated on the “Electrical Conductivity”, some materials are better conductors than others and therefore can offer less resistance to the flow of charge.
4. The fourth variable is related to the purity of the metal and is able to affect the resistance in a manner where the higher the purity of the conductor is, the less the resistance to the flow of the electric charge will be.
A very interesting research conducted by Nakane, H. Watanabe, T. Nagata, C. Fujiwara, S. and Yoshizawa, S. at the Science University of Tokyo, analysed how the reduction of metal’s impurities resulted in a reduction of electrical resistivity. The four scientists based their research on high-purity copper and they measured the resistivity of this metal by implementing a method that estimates resistivity using the difference in the impedance of a circular multilayer solenoid coil with a cylindrical copper core and an identical coil without a copper core (SRPM method). The residual resistivity ratio (RRR) of high-purity copper measured at 100Hz, which is a level that correlates well with the values measured by the DC four-probe method. The results showed the existence of frequency dependences at very low resistivity values for high-purity copper and as the frequency was raised, the skin depth seemed to affect the surface resistivity due to the oxide coating and dirt on the surface of the samples. In addition to that, they discovered that below liquid N2 temperature (77.3K), the resistivity of the copper sample with high purity such as 99.9999% (6N) or 99.99999% (7N) fluctuated at significantly lower levels than that of the copper sample with 99.99% (4N) purity.
Skin Effect
By definition, skin effect is the tendency of alternating currents to flow near the surface of a solid conductor, thus restricting the area that they use to a significantly smaller part of the total cross-sectional area of the conductor. This is causing an increase in the resistance. The major cause of skin effect is the self-inductance of the conductor, which increases the inductive reactance at the relatively higher frequencies of the current, forcing electrons toward the surface of the conductor. Even if skin effect appears mostly in some very high frequency applications like RF power and transmission, it can also attenuate within the frequency range of audio signals, affecting mostly the upper bands. The use of Litz conductors is considered as one of the most effective solutions to the problem. A Litz conductor consists of individually insulated wires (the number of wire and the twist pattern varies depending on the design of each manufacturer), where each of them is less than a skin-depth and therefore they do not suffer from appreciable skin effect losses. Additionally, the fact that the individually insulated wires do not follow the same radial position across the bundle prevents electromagnetic effects that are causing skin effect, helping the conductor to provide lower resistance.
Proximity Effect
This effect is defined as the tendency of a current to flow in loops or concentrated distributions due to the presence of magnetic fields that are generated by nearby conductors.Proximity effect produces an apparent increase in the resistance, especially with high-frequency alternating currents and it is the main cause of imbalanced load distribution. The main symptom of proximity effect in audio, is that it raises the frequency curve around the lower bands, as if someone has turned the “bass knob” clockwise by a quarter of a turn. A solution to this problem can be provided by the use of proper conductor sizes and insulation materials for each application, in combination with an appropriate spacing and an accurate twisting. For some cable applications, the use of Litz conductors may also be a solution to proximity effect.
By wanting to create the optimum cable connections for any type of audio and video device, we have focused our research on the development of hybrid type conductors that can provide increased conductivity and lower resistance, not only due to their metal structure, purity, thickness and cross-sectional area, but also due to their geometry that helps in the further reduction of losses from skin effect and proximity effect.
Hybrid in metal structure
In theory, the use of pure silver would be the optimum choice for any type of conductor, since it is the metal with the highest value of electrical conductivity, which means that it would provide the lowest resistance than any other material at a given thickness, type and length. But in the real world of reproduction electronics where the signal transferring process is so sensitive to numerous parameters, the “recipe” for the optimum signal conductor cannot be as simple as implied by the above – theoretically stable – assumption. At times, numerous equipment reviewers and many more audiophiles have described their own practical experiences of cables based on high purity conductors of a single-metal structure, reporting that even if they realised improvements in many key areas of reproduction, they still did not acquire the anticipated results from the overall performance of their devices. A very frequent example refers to cables with silver conductors, which on the one hand help systems expand their response (mainly at higher frequencies), but at the same time they make them sound slightly emphatic on the upper bands, as if someone has turned the “treble” knob clockwise by a quarter of a turn or even more. Similar impressions are left by many other examples of units connected with copper cables, with users expressing their satisfaction for the performance in the low and medium bands, while at the same time complain about the lack of “air” and “openness” at the higher frequencies.
All these practical examples and a number of tests and scientific investigations made on the properties of copper and silver conductors lead us to the assumption that no conductor of a single metal structure is able to excel in all areas of audio and video reproduction. Challenged by these references and of course by our experiences and measurement results, we focused our efforts on the development of conductors with a hybrid metal-structure from copper, silver and gold. With the proper containment and the lowest possible level of impurities, our conductors will exploit and combine all the advantages of the metals they are made of, creating ideal signal paths for any type of connection.
The relatively lower resistance values at any given thickness and the flat response across the full frequency range, are the major advantages of our conductors that will assist electronic devices to reveal their original characteristics without adding any unwanted coloration.
Hybrid in geometry
There is a large number of home users, reviewers and professionals that show their preference towards cables made of solid wires, believing that this type of conductor is the ideal one for any kind of connection. Many others support that the optimum performance can only be achieved by cables using stranded wires while others insist on using cables based on Litz conductors, aiming to reduce losses caused by skin effect and proximity effect. Aiming to create the ideal signal paths for any type of connection, we invested on the development of conductors with hybrid geometry, which is based on both solid-core wires and stranded wires that are winded with specific patterns (depending on the application) and they are insulated according to the Litz configuration.
The unique geometry of our conductors in combination with their hybrid metal structure produces the optimum signal paths for any type of connection that practically will create this very desirable feeling of coherence, reproducing musical instruments with impressive accuracy and simulating the three dimensions of the stage with outstanding precision.
Insulation

The optimum insulation material would be one with absolutely no response to an electric field and a complete resistance to the flow of an electric charge. Unfortunately though, there is no perfect insulator! On the other hand, there are many materials with very effective insulation properties that can easily outweigh the requirements of many electrical applications, such as the protection of cable conductors. After a thorough research on the electrical and physical properties of many insulation materials, we concluded that the optimum solution for cable conductors would be a combination of such materials. However, before we present the materials we use and the techniques we follow, it would be useful to consider the multiple uses of insulation and how it can affect some major cables characteristics.
A very important role of insulation is to help controlling and maintaining capacitance at the lowest possible levels, so as to keep the unwanted attenuations away from the audible frequency range. This can be achieved by reducing the values of relative permittivity. Theoretically, relative permittivity is a ratio of the amount of electrical energy stored in an insulating material by the voltage that passes through the insulated conductor, in relation to the voltage stored in a vacuum, which is the reference standard insulation. In practice, the values of relative permittivity can be controlled by the type of material (or the combination of materials) that will be used and by their thickness.
Another important use of insulation is to help reducing energy losses that are dissipated as heat. The most accurate indication for these losses can be given by the values of Dissipation Factor. In physics, a Dissipation Factor (DF) is the measurement of the loss-rate of energy of a mode of oscillation (mechanical, electrical, or electromechanical) in a dissipative system. In cable making, the values of a Dissipation Factor can provide a clear view of the dielectric losses in the conductors’ insulation. A low dissipation factor indicates low dielectric losses and this can also be controlled by the proper selection of insulation materials.
At very low frequencies, cables primarily appear inductive and at higher frequencies become capacitive. The Quality Factor is a measurement of how abruptly the change from inductance to capacitance occurs. At the point of transition, the cable is in resonance and so it appears like a pure resistance. But again, with the proper mix of insulation materials, the correct thickness and the overall internal cable design, we can achieve a very high quality factor that practically controls and moves the point of resonance to the right frequencies, helping cables resistance to be ideal and phase response to be more linear. In sound, this is translated into a more natural-sized sound stage, a better clarity and a balanced response across the full frequency range.
In order to achieve the maximum protection for our conductors, to keep relative permittivity and dissipation factor at the lowest possible levels, to score the highest possible values of quality factor and in the same time to provide a quite satisfactory flexibility, we have developed specific insulation techniques for each type of cable that we produce, based on multi-layer designs. The materials we use are presented on the board below:
Shielding
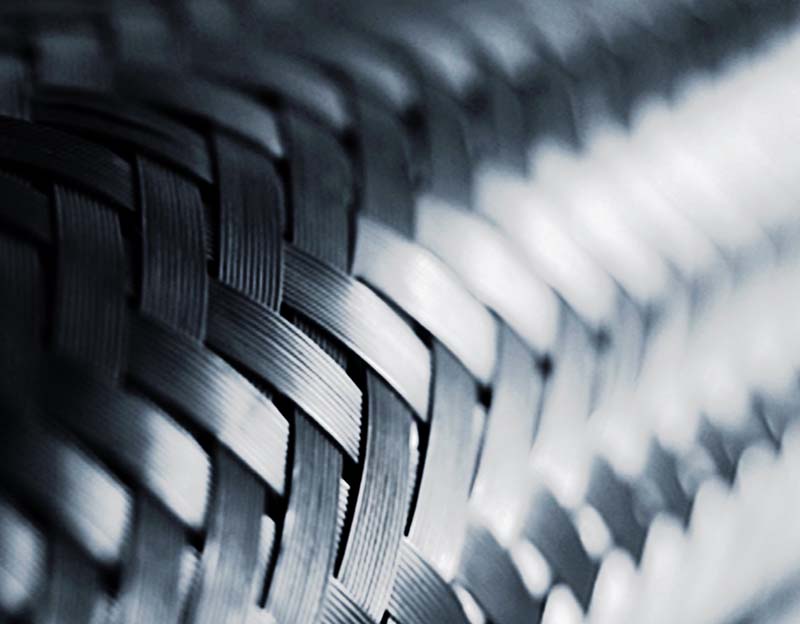
Since the early days of radio communications, all engineers and circuit designers of the industry inevitably engaged on a battle against the unwanted effects of radiated interferences. This battle continues even in our days, where the significantly increased number of external sources of radiation, the complexity of today’s electronic circuits and the increased number of connections, are causing consistent problems to the engineers of the audio and video industries.
All these problems are encapsulated in two main forms of interferences, namely Electromagnetic Interferences (EMI) and Radio Frequency Interferences (RFI).
Aiming to the maximum protection against all kinds of emitted interferences, we have developed various patterns for each cable type we produce, based on combinations of aluminum foil, braided copper and French BraidTM.
Additional protection against magnetically coupled inteferences is provided by the impressively low transferred impedance values of our cables and of course by the accurate response across the audible frequency range, which is absolutely free from unwanted noises.
An Electromagnetic Interference may appear either as an unwanted induction, or as an electrical or electronic disturbance which is emitted either from external or from internal sources, affecting negatively the response and consequently the overall performance of circuits and cables.
A Radio Frequency Interference, as the abbreviated words describe it, is any undesirable electrical energy with negative effects in the range of radio frequency transmissions. There are two main categories of RFI. The radiated, which is mostly found in the frequency range between 30MHz and 10GHz, and the conducted which is oscillating inside the audible frequency range (usually on the upper bands) and up to 30MHz. In our field, both Electromagnetic and Radio Frequency interferences can become equally harmful to the total performance of cables, since they can use them either as a source of interference by conducting noise to the connected equipment, or as a receiver by using cables to pick up the emitted interferences from other sources.
This is the reason why shielding is one of the main factors to determine the performance of both signal-carrying and power-carrying cables. The effectiveness of any given shielding configuration can be evaluated by the transfer impedance test. This method is the most widely accepted for evaluating the shielding performance of a cable against ESD and radiated emissions coupling at frequencies from DC to 1000 MHz and is recommended by the International Electrotechnical Commission as well as the military.
EMI and RFI can become equally harmful to the total performance of cables.
In measurement terms, the lower the transfer impedance value is, the more effective the shielding configuration of the cable is. In practice, there are various shielding configurations and each of them offers different levels of efficiency.
An Electromagnetic Interference may appear either as an unwanted induction, or as an electrical or electronic disturbance which is emitted either from external or from internal sources, affecting negatively the response and consequently the overall performance of circuits and cables.
A Radio Frequency Interference, as the abbreviated words describe it, is any undesirable electrical energy with negative effects in the range of radio frequency transmissions. There are two main categories of RFI. The radiated, which is mostly found in the frequency range between 30MHz and 10GHz, and the conducted which is oscillating inside the audible frequency range (usually on the upper bands) and up to 30MHz. In our field, both Electromagnetic and Radio Frequency interferences can become equally harmful to the total performance of cables, since they can use them either as a source of interference by conducting noise to the connected equipment, or as a receiver by using cables to pick up the emitted interferences from other sources.
This is the reason why shielding is one of the main factors to determine the performance of both signal-carrying and power-carrying cables. The effectiveness of any given shielding configuration can be evaluated by the transfer impedance test. This method is the most widely accepted for evaluating the shielding performance of a cable against ESD and radiated emissions coupling at frequencies from DC to 1000 MHz and is recommended by the International Electrotechnical Commission as well as the military.
In measurement terms, the lower the transfer impedance value is, the more effective the shielding configuration of the cable is. In practice, there are various shielding configurations and each of them offers different levels of efficiency. The most common shielding types of today are:
Foil shield
This type of shielding consists of an aluminum foil and a film layer of polypropylene which is used to add strength and prevent foil from shredding. The main advantage of foil shielding is the increased level of protection from the emitted interferences due to the fact that it provides 100% coverage of the conductor’s insulation surface. The disadvantage of foil shielding is the relatively increased resistance compared to a braid shield, and this is the reason why aluminium foils cannot provide equally effective grounding.
Braid shield
The braid shielding is a woven mesh of bare or tinned copper wires, which offers a greater structural integrity and increased flexibility compared to aluminium foil shielding. Besides that, the main advantage of braid shielding is the very low DC resistance compared to aluminium shielding, a fact that makes it ideal for grounding. Another advantage of a braided shield is its ability to minimize interference at low frequencies. On the other hand, braided shields cannot cover the complete surface of a cable, even when the woven mesh is very tightly braided. Due to this specific structural characteristic, braided shields cannot offer 100% protection from the emitted interference.
Foil / Braid shield
Combination shields consist of more than one layer of shielding and provide maximum shield efficiency across the frequency spectrum. The foil/braid shield combines the advantages of 100 percent foil coverage with the strength, the flexibility and the very low DC resistance of a braid.
French Braid shield
This type of shielding was developed especially for audio and RF cable applications. It is a very flexible double spiral design, consisting of two bare or tinned copper wires in a spiral form, tied together by one weave across the full length of the cable. The French BraidTM shielding offers a longer flex life than the standard spiral shields, and it is a lot more flexible than the conventional braid shields. It produces a much lower level (approx. 50% less) of microphonic and triboelectric noises than the conventional braid shields and an even better performance than the single spiral, due to the relatively lower DC loop resistance.
There are many ways that Radio Frequencies can be induced on shielded cables. However, the most common situations of RF induction into signal conductors are:
– When the shields of cables are based only on the braid and not on the foil/braid configuration, where there is a great possibility for coupling of electric fields through tiny openings in the braided shield. The same action can occur when cables are shielded with poor quality aluminium foil that is usually torn when cables are bent at extreme angles.
– In situations where there is an imbalance of the capacitances between the signal conductors and the shield, then voltage gradients may be caused affecting signal conductors and consequently the overall performance of the system.
– The situation of an imbalance in the magnetic coupling between the shields of cables and signal conductors increases significantly the chances for noise induction. This mechanism was named Shield Current Induced Noise and was widely analysed by a few great researchers like Neil Muncy, the Eastern Vice President of AES, Jim Brown of Audio Systems Group and Bill Whitlock of Jensen Transformers, with some very interesting conclusions.
More specifically, Neil Muncy performed a number of tests on many cables with different shielding configurations and by driving their shields with a specific current he firstly proved that the audio frequency current that flows on the shield of twisted-pair cables will be converted into differential mode voltage on the signal pair, and secondly he measured a relatively higher shield current induced noise on the signal conductors of cables with poorer shield configuration.
Based on the results of Neil Muncy’s research, the foil/drain-shielded cables had the worst SCIN performance, the braid-shielded cables were about 30 dB better and the foil/braid-shielded cables with no drain wires had by far the best SCIN performance. In addition to the above, Jim Brown and Bill Whitlock reassured the conclusions of Neil Muncy’s research by proving that the current which flows on the shield of twisted-pair cables produces a corresponding differential mode voltage on the twisted pair that is proportional both to the frequency of the current as well as to the length of the cable (and therefore to its inductance), for all cables that are shorter than the 1/20 of the wavelength of the interfering signal. They also drew a number of other crucial assumptions, and below we make a reference to those who are closely related to our field, as they were printed on their research:
– Between 1/20 and 1/10 wavelengths, the SCIN will continue to increase approximately in proportion to frequency and cable length. However, when a cable is longer than 1/10 wavelength at the frequency of the interfering current, then some frequency-dependent terms will dominate and it will be very difficult to predict SCIN.
– The SCIN appears to include an additive term whose magnitude is approximately proportional to the fraction of the shield current that flows through a drain wire to the total shield current. The data suggests that the maximum degradation caused by a drain wire is approximately 25-30 dB.
– The SCIN appears to include algebraically additive reactive terms that result from imbalances in the lengths of the signal conductors, imbalances in the inductance of the signal conductors, and imbalances in the capacitances between the signal conductors and the shield. These reactive components have both positive and negative signs, because a) magnitude and phase of voltages and currents vary along the length of a cable longer than 1/20 wavelength, and b) the mechanism that produces current is so variable from one installation to another, making the prediction of these terms very complex.
– For cables less than 1/10 in wavelength at the frequency of the shield current, reactive factors are insignificant for foil/drain-shielded cables, and relatively low in influence with braid/drain shielded cables. For foil/drain-shielded cables, SCIN attributable to the drain wire is in the region of 20-30 dB greater than SCIN attributable to other factors. And for most braid-shielded cables having a drain wire, SCIN attributable to the drain wire is more or less 10 dB greater than SCIN attributable to other factors.
– Any asymmetry in the termination of a cable can degrade SCIN performance. This is most significant with cables having relatively good SCIN characteristics. In addition to that, manufacturing tolerances should be expected to cause variations to the SCIN performance from one sample to another of braid-shielded cable.
Based on the combination of Foil/Braid shields and of Foil/French BraidTM shields, we have designed specific shielding configurations for each type of cable that we produce, achieving the maximum protection from all kinds of emitted interferences. Additional protection against magnetically coupled interferences is also provided by the twisted pair structure of our conductors.
The appropriate number of twists per unit length and the accurate uniform continuation is helping our cables to achieve a very effective noise rejection. The efficiency of our shielding configurations and of our twisted pair structures can be proved by the impressively low transferred impedance values of our cables and of course by the accurate response across the audible frequency range, which is absolutely free of hiss and hum noises.
Grounding
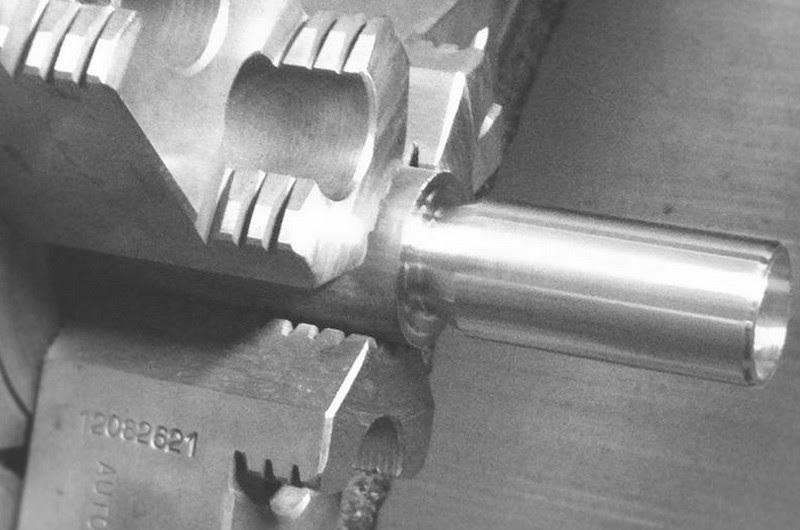
In cable making, the term “ground” refers to the physical ending of the shield, which for some cable types, is connected on both ends, for others it is connected only on one end, and for a few other types of cables the shield is grounded directly to external points. In all cases, the grounding configuration is a determinant factor for the effectiveness of the shield and thus for the overall performance of the cable. The grounding of cables is called to play two key roles. Firstly, to create a path between the shield and the connected device in order to help discharging all unwanted signals and noises that have been intercepted by the shield, and secondly, to create directional conducting paths between the grounds of all connected devices, so as to guide ground currents to earth. Before we proceed to the description of the grounding solutions we follow and apply to our cable designs, it would be very helpful to examine some of the problems that may appear and affect the performance of a system due to improper grounding.
In Signal Projects we apply some of the most efficient grounding techniques for each cable type we produce, creating directional paths of very low resistance, that practically cancelling ground loops and in the same time are properly discharging noise current and travelling across the shields.
One of the most difficult problems to diagnose and resolve in a system of audio and video components is called ground loop. Ground loop occurs when two or more electronic devices are using more than one connection path to reach common ground, creating this way a closed “loop” circuit through which, ground currents of different potential may flow. In such a case, the electrical level of the shields, which is normally varies form very low to zero volts, starts to fluctuate above and below zero with a significant difference in voltage, causing interference on the transferred signal
A very common example of ground loop in an audio system is when, ground currents of two or more connected units “meet” on multiple paths that are created by the ground wires of power cables and the negative signal conductors of the single-ended interconnect cables that are operating also as ground paths between the connected units. The ground currents that flow through this closed loop circuit are usually generated by voltage differences, inductions from cables and devices, poor cable shielding, other wiring errors, ground faults, and normal leakage. In practice, various problems may appear as a result of ground loop, starting from simple noises, up to major component damage. In all cases, the role of cables is very important since they are integral parts of a system, and thus will also be parts of any ground loop that may be created, either as “causes” of the problem or as “victims” of it. The most frequent problems caused by ground loops are:
– In a ground loop circuit, the connected devices are usually producing currents of different potential. These currents may induce voltages in the audio circuitry of electronics and in the signal conductors of cables, causing hum noises at 60Hz or 50Hz (depending on each country’s AC frequency), and some other times electrical noises at higher frequencies.
– A ground loop can also be one of the main causes of common-mode noise. Common mode noise is the electrical interference which is induced on all signal or all power line conductors of a cable in the same direction. In a case of ground loop circuit, where currents are flowing continuously in one direction across the shields and ground wires of cables, a common mode noise could be developed.
The specific resistance of ground wires and shields will cause voltages that inevitably are induced to the internal conductors, affecting the signal. The higher the shield or ground wire resistance is, the greater the voltage will be. Another example is when ground currents flow continuously on the direction through the ground wire of a power cable, affecting this way the line and neutral carrying conductors. In both cases, this noise is injected into the audio circuitry (through interconnect cables) and even worse into the power supplies (through the power cables), affecting the performance of devices.
– Another problem that may be created in a ground loop circuit is when some switching or inrush currents inside electronic devices are producing transients of high energy. These transients usually prefer to travel on their way to earth through the grounded shields of interconnect cables instead of the ground wires of power cables, a fact that may affect audio signals and in some cases where the surge is high enough it may cause serious equipment damage.
A very frequent problem that may affect unbalanced and poorly shielded interconnect cables, is the antenna action. This action usually occurs on cables which are grounded on one end and their grounding configuration is proved improper and unable to discharge effectively the noise currents from the shield. In such a case, the RF signals are using the cable as an antenna, by increasing voltage along the shield. This voltage takes the form of common mode component, with the unwanted result of affecting conductors that carry audio signals.
By aiming at the most effective discharge of noise currents from the shields of our cables, we have designed specific grounding configurations according to the requirements of each cable type.
Unbalanced interconnections
The traditional unbalanced interconnects are structured with one conductor and shield. In this configuration, the conductor is the carrier of positive signals and the shield is acting both as the negative path and the grounding path between the source device and the receiver device. Due to this structural characteristic, all traditional unbalanced interconnects are more vulnerable to ground loops that can be created when there is an increased potential in one of the two connected chassis.
The most effective solution to this problem can be provided by the use of balanced cable designs that can even be applied to unbalanced type connections. In this case, one conductor is used for the positive voltage, the other conductor is used for the negative voltage and the shield is usually grounded either on the input termination, or the output termination. In Signal Projects, our unbalanced interconnect cables are based on exactly the same internal geometry and cable design with our balanced interconnect cables.
More specifically, for the construction of our unbalanced interconnects we use a truly balanced configuration with two conductors of the same cross sectional area, of the same type, of the same metal and of the same purity for both the positive and negative paths. These conductors are protected by exactly the same shielding materials that we use on our balanced cables, with the only difference being on the grounding, which in this case is connected on the “output unit” termination.
The reason why we follow this specific grounding configuration is because a) in most cases the noise currents will find better grounding circuits with lower impedances as they go downstream from the sources to pre-amplification units and from the pre-amplification units to power amplifiers, and b) we believe that it is more preferable to guide ground currents to the units with the lowest possible gain amplification.
Balanced interconnections
Theoretically, the use of balanced cables would offer the best interconnecting solution for any audio and video device. Practically, this assumption would only be stable if the connected devices were based on entirely differential balanced circuits with proper grounding configurations.
Unfortunately, there are many audio and video devices which, even though offer the option of balanced input and output connections, they are based on pseudo-balanced circuits, which means that the truly balanced signal “before entering into” and “before exiting from” the processing circuitry, passes through transformers or additional amplifier stages in order to be converted from balanced to single-ended and from single-ended to balanced respectively.
This additional conversion path usually brings negative results in the overall performance of a system, since it is practically “canceling” the main role and the advantages of balanced cables and thus the advantages of a truly balanced topology. In most of these cases, the performance of balanced connections does not provide the expected results and the worst thing is that cable manufacturers cannot magically change the conflicting situation created by pseudo-balanced devices. On the other hand, the existence of some pseudo-balanced devices should never deflect cable makers from the original design characteristics of balanced cables.
In Signal Projects we are well aware of that and this is the reason why we strictly adhere to the basic design principles of balanced cable designs.
– One of these is the fundamental design characteristic of balanced cable structures, which is the use of one conductor for the positive, one identical conductor for the negative and a shield that is grounded on Pin 1 of both ends. This is the basic design configuration of balanced cables that, when connecting a system of truly balanced devices, has proved to be much less sensitive and vulnerable to ground loop problems because a) the shield is used as a dedicated path for the ground currents, and b) the differential transmission of signals is achieving a very effective noise rejections across the audible frequency range.
– Another characteristic of our balanced cables is the use of high quality braided copper shields that offer very low resistance to ground currents that will travel through the shield. The combination of aluminium foil with a properly grounded low resistance braided shield can offer excellent protection from the emitted interferences and a very effective noise current discharge.
– Even in balanced cables, a directional ground path would be very effective against the creation of ground loops. During the past years, many cable makers experimented with various techniques aiming to give a specific direction to the noise currents that move across the shields of balanced interconnect cables. One of these techniques was to solder between Pin 1 and the one end of the shield, a small resistor in parallel with a small capacitor.
This method offered satisfactory filtration for the interferences and also increased the resistance in one end of the grounded shield, guiding this way the noise currents to the other end with the lower resistance. In some cases, this technique proved effective. However, the existence of a capacitor on the ground path was always a risky venture, since in some cases it may even cause a shock hazard. Additionally, even that small increase in the resistance of “Pin 1 path” could influence the dumping factor of truly balanced amplifiers creating a number of negative results in their circuitry operation and consequently on their sounding performance.
Another technique that some cable makers applied in order to create directional ground paths through the shields of balanced interconnects was to connect the shield only on one end of the cable. On the one hand this method proved effective in the creation of directional ground paths, but on the other hand it was canceling the original structure of balanced cables and thus it was becoming inappropriate for all truly balanced devices. A further technique was based on a small circuit of diodes that was connected on one end of the shield. The configuration of this circuit was able to “open the doors” of the shield in both directions for all incoming ground currents (which means that it was not canceling the truly balanced topology) while at the same time, it managed to keep the “doors closed” on the one end for the currents that had already entered the shield.
The problem was that this technique was ideal mostly for custom applications, since the small circuit of diodes operated with specific currents and thus couldn’t be followed by any manufacturer who wanted to produce identical balanced cables for all balanced devices. Finally, we couldn’t end this section without referring to the most common technique that many DIY audio enthusiasts and even more professionals have followed and still follow in order to resolve ground problems. This technique is based on transformers which are usually placed on one end of balanced cables and they are connected both to signal conductors and to the shield, offering excellent results against ground problems.
However, even if this method proved to be very effective, we cannot imagine a cable maker who has invested large amounts of money researching into the optimum combination of metal purities, conductor types and thicknesses, aiming at the most pure signal transferring, to cancel the results of his research by interpolating transformers between signal conductors.
After conducting many tests on the above mentioned techniques and after a very careful evaluation of their positive and negative aspects, we decided to follow a simple but very effective method in order to create directional ground paths on the shields of balanced cables, without affecting the fundamental characteristics of a truly balanced structure.
This method is applied inside the termination modules of our cables and it is based on a specific configuration of conductive materials that are used primarily to connect the shield with Pin 1 of both plugs and secondly to maintain a relative difference in the resistance values of these two ground connections. Knowing that noise currents tend to follow directions that lead to connections of an even slightly lower resistance, in our balanced cables the ground connections of female plugs will always provide a higher resistance than those of male plugs, because – as we mentioned above in the section of Unbalanced Interconnections – we believe that it is preferable to guide ground currents to the units with the lowest possible gain amplification.
Digital Interconnections
In most system setups, the reactive current that floats across the shield of digital audio connections is not high enough to harm the digital signal. However, in cases where a ground loop circuit is created and noise currents are sufficient enough to corrupt digital data by affecting their flow (increase of jitter levels), we may experience negative symptoms like hum noises between 50Hz and 60Hz, digital whistles at higher frequency ranges and even some irritating colorations in the mid-band.
In order to achieve maximum performance and at the same time to provide maximum protection against ground loops and externally induced interferences, we have built our digital cables according to the geometry and the grounding configuration of our analog interconnects. More specifically, both our balanced and unbalanced digital cables are based on balanced cable structures with one conductor for the positive, one for the negative and one shield. With regard to the balanced digital interconnects, the shield is grounded on both ends of the cable according to the AES/EBU standards and in order to create a directional ground path on the shield of the cable, we apply exactly the same method that we described above in the section of “Balanced Interconnections”.
Concerning our unbalanced digital interconnects, we do not follow the common co-axial cable structure that uses one conductor for the positive signal and a shield for both negative signal and ground, since we gained much better results with the use of a balanced cable structure and by having the shield connected only on the output plug, creating a directional ground path that leads to the receiver unit. The reasons why we chose the specific cable geometry and grounding configuration are presented above in the section of “Unbalanced Interconnections”.
Power cables
There are two types of noises that are closely related to power cables which are usually induced on nearby interconnects and more frequently on the connected devices, negatively impacting the system’s performance.
The first type is called Differential Mode Noise and it occurs on the Line and the Ground in opposite directions to each other, and the second type is Common Mode Noise which is occurs on all lines in the same direction. These noises are usually produced inside a ground loop circuit either due to currents of a different potential and opposite direction, or due to very high potential currents that pass through the shields of poorly made cables, affecting both line and neutral conductors.
A number of solutions like the use of transformers or common-mode chokes have been tested in many applications, resulting in the reduction and even in the elimination of these noises, while a proper and accurate twisted pair design always helped opposing currents to be wounded uniformly and to produce equal and opposite polarized magnetic fields that would end up cancelling each other out. Undoubtedly, the above solutions proved to be the ideal ones for some applications.
On the other hand though, we prefer to avoid the use of transformers and chokes in cables that will be used to connect high fidelity reproduction devices, due to a number of reasons which are mostly related to signal distortion. After many tests on various system setups and while at the same time being focused on the elimination of common and differential mode noises, as well as any kind of electromagnetic interference, we developed a sophisticated design for all our power cables which is based on the use of three completely isolated conductors with a completely independent shielding and grounding configuration for each one of them.
The shield of each conductor is grounded only on the male plug and not on the IEC plug due to three main reasons. Primarily, because we want to create directional ground paths towards the earth in order to safely and rapidly guide all noises that are blocked by the shield. Secondly, because we want to completely eliminate the possibility of a ground loop creation in the shields of the cable and thirdly, because we prefer to use only the ground conductor as the main connection between the earth and the unit’s ground, avoiding all these unwanted situations where ground currents of the circuit use the shield of Line and Neutral conductor to travel to earth.
Finally, in combination with this highly effective geometry, the use of proper ferrites will provide additional protection against all types of noises, making our power cables the optimum solutions for any system application.